Algorithmic materials discovery is a multidisciplinary domain that integrates insights from specialists in alloy design, synthesis, characterization, experimental methodologies, computational modeling, and optimization. Central to this effort is a robust data management system paired with an interactive work platform. This platform should empower users to not only access others’ data but also integrate their analyses, paving the way for sophisticated data pipelines. To realize this vision, there is a need for an integrative collaboration platform, streamlined data sharing and analysis tools, and efficient communication channels. Such a collaborative mechanism should transcend geographical barriers, facilitating remote interaction and fostering a challenge-response dynamic. To further enhance precision and interoperability in this multifaceted research landscape, we must explore innovative ways to refine these processes and improve the integration of expertise and data across diverse domains. In this paper, we present our ongoing efforts in addressing the critical challenges related to an accelerated materials discovery framework as a part of the High-Throughput Materials Discovery for Extreme Conditions (HTMDEC) Initiative. Our BIRDSHOT (Batch-wise Improvement in Reduced Materials Design Space using a Holistic Optimization Technique) Center has successfully harnessed various tools and strategies, including the utilization of cloud-based storage, a standardized sample naming convention, a structured file system, the implementation of sample travelers, a robust sample tracking method, and the incorporation of knowledge graphs for efficient data management. Additionally, we present the development of a data collection platform, reinforcing seamless collaboration among our team members. In summary, this paper provides an illustration and insight into the various elements of an efficient and effective workflow within an accelerated materials discovery framework while highlighting the dynamic and adaptable nature of the data management tools and sharing platforms.
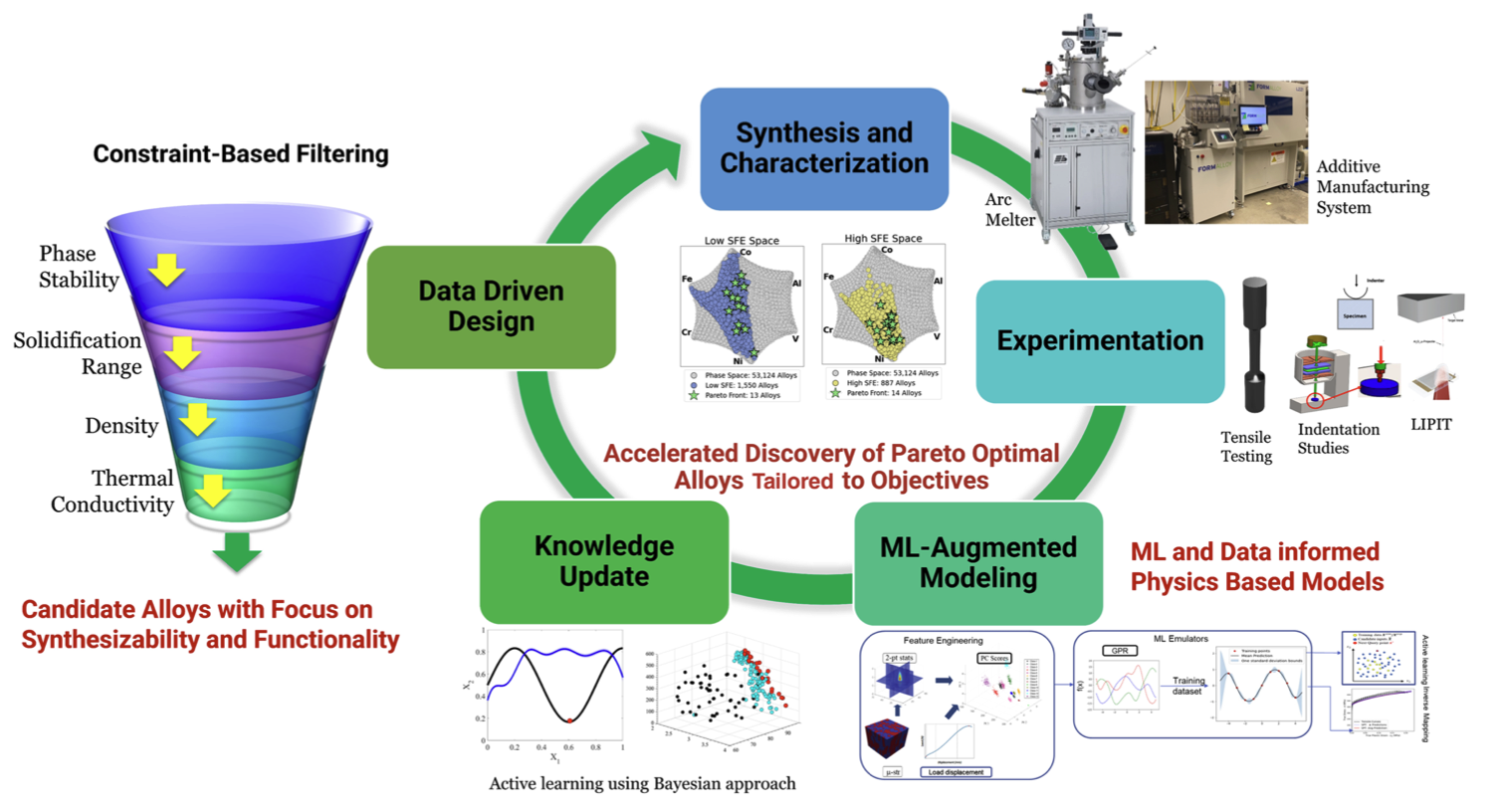
Closed-loop materials discovery and optimization framework designed for BIRDSHOT showing the integration of main thrusts of interest